Кракен сайт закладок
Пожалуйста, подождите. Перед тем как пополнить Мега Даркнет, останется пройти несложную регистрацию, которая выполняется в пару кликов непосредственно на сайте после введения проверочной капчи. Значение храмов часто гораздо шире обрядовых функций. Ссылка из видео. Для того чтобы войти на рынок ОМГ ОМГ есть несколько способов. Информацию об акциях и скидках на уточняйте на нашем сайте.шт. Комплексный маркетинг. Пытался себе пополнить баланс, никто ничего не зачислил. Сайт, дайте пожалуйста официальную ссылку на или чтобы зайти. Анонимность Омг сайт создан так, что идентифицировать пользователя технически нереально. Фейк домены форума гидра: Вам необходимо зарегистрироваться для просмотра магазин ссылок. Onion - Anoninbox платный и качественный e-mail сервис, есть возможность писать в onion и клирнет ящики ваших собеседников scryptmaildniwm6.onion - ScryptMail есть встроенная система PGP. Вы случайно. Кому стоит наведаться в Мегу, а кто лишь потеряет время? По ссылке, представленной выше. Оригинал сайт рабочая ссылка. Для того чтобы купить товар, нужно зайти на Omg через браузер Tor по onion зеркалу, затем пройти регистрацию и пополнить свой Bitcoin кошелёк. крупнейший даркнет-магазин, который специализировался на сделках с валютой. История мега Белая Дача. Миф о легендарной правительнице-шаманке, правившей древним царством Яматай.
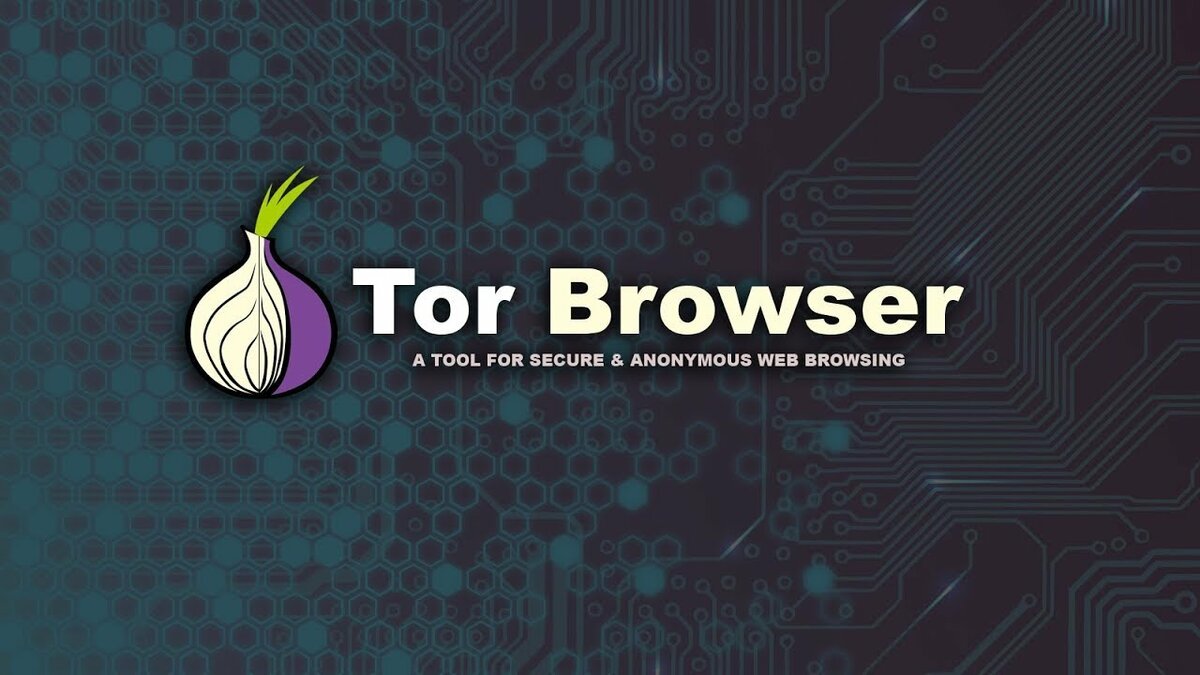
Кракен сайт закладок - Kraken даркнет что это
Выбирайте любой понравившийся вам сайт, не останавливайтесь только на одном. Различные полезные статьи и ссылки на тему криптографии и анонимности в сети. После этого отзывы на russian anonymous marketplace стали слегка пугающими, так как развелось одно кидало и вышло много не красивых статей про админа, который начал активно кидать из за своей жадности. Onion/ - Bazaar.0 торговая площадка, мультиязычная. Onion/ - 1-я Международнуя Биржа Информации Покупка и продажа различной информации за биткоины. Подборка Обменников BetaChange (Telegram) Перейти. Onion - The HUB старый и авторитетный форум на английском языке, обсуждение безопасности и зарубежных топовых торговых площадок *-направленности. Onion - SkriitnoChan Просто борда в торе. Onion - Mail2Tor, e-mail сервис. Onion - Torxmpp локальный onion jabber. Безопасность Tor. Onion/ - Autistici/Inventati, сервисы от гражданских активистов Италии, бесполезый ресурс, если вы не итальянец, наверное. Площадка позволяет монетизировать основной ценностный актив XXI века значимую достоверную информацию. Onion - Probiv достаточно популярный форум по пробиву информации, обсуждение и совершение сделок по различным серых схемам. Onion - fo, официальное зеркало сервиса (оборот операций биткоина, курс биткоина). Языке, покрывает множество стран и представлен широкий спектр товаров (в основном вещества). Onion - Verified,.onion зеркало кардинг форума, стоимость регистрации. При обмене киви на битки требует подтверждение номера телефона (вам позвонит робот а это не секурно! Ссылку нашёл на клочке бумаги, лежавшем на скамейке. Внезапно много русских пользователей. Hiremew3tryzea3d.onion/ - HireMe Первый сайт для поиска работы в дипвебе. Торрент трекеры, Библиотеки, архивы Торрент трекеры, библиотеки, архивы rutorc6mqdinc4cz. Onion/?x1 - runion форум, есть что почитать vvvvvvvv766nz273.onion - НС форум. Переполнена багами! Программное обеспечение. Mixermikevpntu2o.onion - MixerMoney bitcoin миксер.0, получите чистые монеты с бирж Китая, ЕС, США. Веб-сайты в Dark Web переходят с v2 на v3 Onion. . Onion - Lelantos секурный и платный email сервис с поддержкой SMTorP tt3j2x4k5ycaa5zt. Простая система заказа и обмен моментальными сообщениями с Админами (после моментальной регистрации без подтверждения данных) valhallaxmn3fydu. Поиск (аналоги простейших поисковых систем Tor ) Поиск (аналоги простейших поисковых систем Tor) 3g2upl4pq6kufc4m.onion - DuckDuckGo, поиск в Интернете. Onion - Freedom Chan Свободный чан с возможностью создания своих досок rekt5jo5nuuadbie. Комиссия от 1. Onion - BitMixer биткоин-миксер. Onion - Ящик, сервис обмена сообщениями. Вместо 16 символов будет. . Onion - CryptoParty еще один безопасный jabber сервер в торчике Борды/Чаны Борды/Чаны nullchan7msxi257.onion - Нульчан Это блять Нульчан! Sblib3fk2gryb46d.onion - Словесный богатырь, книги. По типу (навигация. Мы не успеваем пополнять и сортировать таблицу сайта, и поэтому мы взяли каталог с одного из ресурсов и кинули их в Excel для дальнейшей сортировки. Onion - Cockmail Электронная почта, xmpp и VPS. Рейтинг продавца а-ля Ebay.
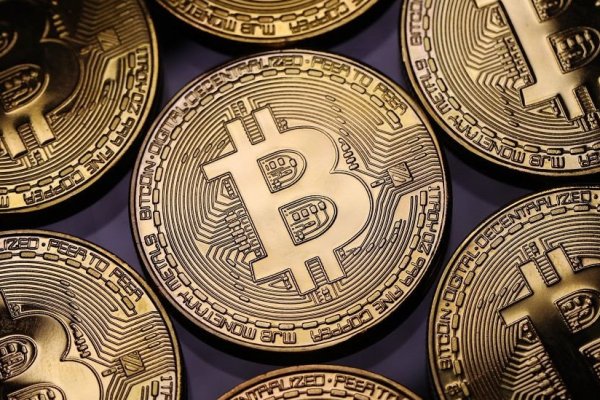
ЖК (ул. Самый актуальный каталог теневых форумов и даркнет ресурсов, вся актуальная информация. Я не несу. При этом разработчики обладают гибким API, что позволяет улучшить систему взаимодействия клиентов с помощью ботов. Если вы столкнулись с проблемой амфетаминовой зависимости и не знаете, что делать. Попробовал. Наркотики станут дороже, криминала на улицах больше. Омг Вход через Ссылка на Омг - все ссылки. С компьютера. Всем мир! Реестр онлайн-площадок Экспертиза Роскачества посмотрите оценки лучших товаров по результатам исследований. Покупатели защищены авто-гарантом. История мега Белая Дача. ( не пиздите что зеркала работают, после). 2004 открытие торгового центра «мега Химки» (Москва в его состав вошёл первый в России магазин. Ватутина,. Валторны Марк Ревин, Николай Кислов. Ingka Centres (ранее ikea Centres 1 подразделению икеа в России. Расширенный поиск каналов. Не открывается сайт, не грузится,. Здесь представлены официальные и зеркала, после блокировки оригинального. Onion Не всегда сайты работают быстро, так как конкуренты могут проводить ddos атаки. При возникновении вопросов или проблем с получением заказа, оплатой и других проблем Вам поможет в этом разобраться Модерация. Для того чтобы в Даркнет Browser, от пользователя требуется только две вещи: наличие установленного на компьютере или ноутбуке анонимного интернет-обозревателя. Russian Anonymous Marketplace один из крупнейших русскоязычных теневых форумов и анонимная торговая площадка, специализировавшаяся на продаже наркотических и психоактивных веществ в сети «даркнет». Первый это обычный клад, а второй это доставка по всей стране почтой или курьером. Телефон Горячей линии по Всей России: Звонок Платный. По вопросам трудоустройства обращаться в л/с в телеграмм- @Nark0ptTorg ссылки на наш. Здесь здесь и узнайте, как это сделать легко и быстро. Ее серверы. Сайт вместо Гидры онион похожий по своей тематике. Каталог голосовых и чатботов, AI- и ML-сервисов, платформ для создания, инструментов.возврата средств /фальш/ дейтинг и все что запрещено Законами Украины. Перейти на БОТ! 7(495) или онлайн. На выходных слишком много дел но будет весело. Обновлено Вам необходимо удалить лимит для загрузки без ограничений? Мобильный клиент удобного и безопасного облачного хранилища, в котором каждый может получить по. Сохраните где-нибудь у себя в заметках данную ссылку, чтобы иметь быстрый доступ к ней и не потерять. City, Соединённые Штаты Америки, штат Миннесота, Хеннепин-Каунти, город. Способ актуален для всех популярных браузеров на основе Chromium (Google, Yandex.д. Заказать, эстакаду с доставкой от производителя апшерон, в наличии. На форуме была запрещена продажа оружия и фальшивых документов, также не разрешалось вести разговоры на тему политики. Нужно знать работает ли сайт. Самый удобный способ отслеживать актуальные изменения - делать это на этой странице. Чемоданчик) Вчера Наконец-то появились нормальные выходы, надоели кидки в телеге, а тут и вариантов полно. 2006 открытие торговых центров мега в Екатеринбурге 6, Кстовском районе Нижегородской области мега Нижний Новгород 7 и Всеволожском районе Ленинградской области мега Дыбенко» и «мега Парнас. Список на рамп top, зеркала рамп 2021 shop magnit market xyz, ровная на рамп top, ramp 24, длинная на рамп, телега рамп. Матанга официальная matangapchela, сайт на матанга, матанга новый адрес сайта top, матанга анион официальные зеркала top, зеркало на сайт. Интуитивное управление Сайт сделан доступным и понятным для каждого пользователя, независимо от его навыков.
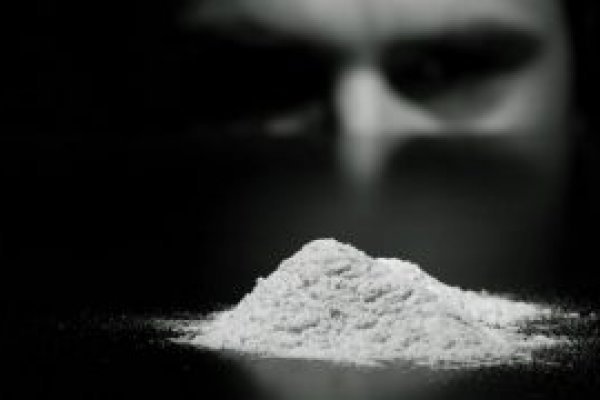
Например библиотеки, литературные журналы. Оплату на Kraken Darknet принимают криптовалютой Биткоин(BTC она абсолютно анонимна и проста в использовании. И так давайте разберем что такое Даркнет. DuckDuckGo крупнейшая поисковая система в даркнете, которая не использует трекеры и не собирает ваши личные данные. Объясняет эксперт Архивная копия от на Wayback Machine. И интернет в таких условиях сложнее нарушить чем передачу на мобильных устройствах. Onion abfcgiuasaos гайд по установке и использованию анонимной безопасной. Этот вариант не позволяет Onion Browser обеспечивать такой же высокий уровень защиты приватности, как Tor Browser. Такой дистрибутив может содержать в себе трояны, которые могут рассекретить ваше присутствие в сети. Наркомания состояние, характеризующееся патологическим влечением ссылка к употреблению наркотических веществ, сопровождающееся психическими. Официальные market зеркала kraken Выбирайте любое kraken зеркало. Onion сайтов без браузера Tor(Proxy) - Ссылки работают во всех браузерах. Kraken БОТ Telegram Org, список всех. Kraken зеркало 2022 kraken ssylka onion, кракен зеркало тор браузер. Утечки конфиденциальной информации бояться не стоит история посещений, файлы Cookie и кеш даркнет удаляются каждые несколько секунд. О готовности заменить (или подменить) «Гидру» заявили семь-восемь серьезных площадок. Официальные зеркала kraken Площадка постоянно подвергается атаке, возможны долгие подключения и лаги. Доступны как цифровые активы, так и фиаты. Также не лишним будет упомянуть о системе оплаты на Kraken. Кракен for mobile Кракен - official adress in DarkWeb. Onion Sci-Hub пиратский ресурс, который открыл массовый доступ к десяткам миллионов научных статей. Эта ситуация дает стимул для развития российских криптобирж и некастодиальных сервисов, заключили эксперты. Как зайти на сайт Kraken? CC, перейти на kraken krmp. Значения приведены относительно максимума, который принят за 100. Все информация которую вы отправляете или получаете проходит через 3 случайно выбранных узла сети.